How Wood Lamination Machines Operate
Unlike standard laminators, woodworking variants are engineered to handle the unique properties of wood, such as grain variations, porosity, and susceptibility to environmental changes. They bond laminates—thin layers of plastic, vinyl, or resin-based films—to wood substrates using heat-activated adhesives or pressure-sensitive systems. Advanced models feature adjustable pressure rollers (up to 50 psi) and precision temperature controls (typically 100–200°C) to accommodate diverse materials, including heat-sensitive veneers and high-pressure laminates (HPL). Some machines integrate edge banding functions for seamless side-surface coverage.
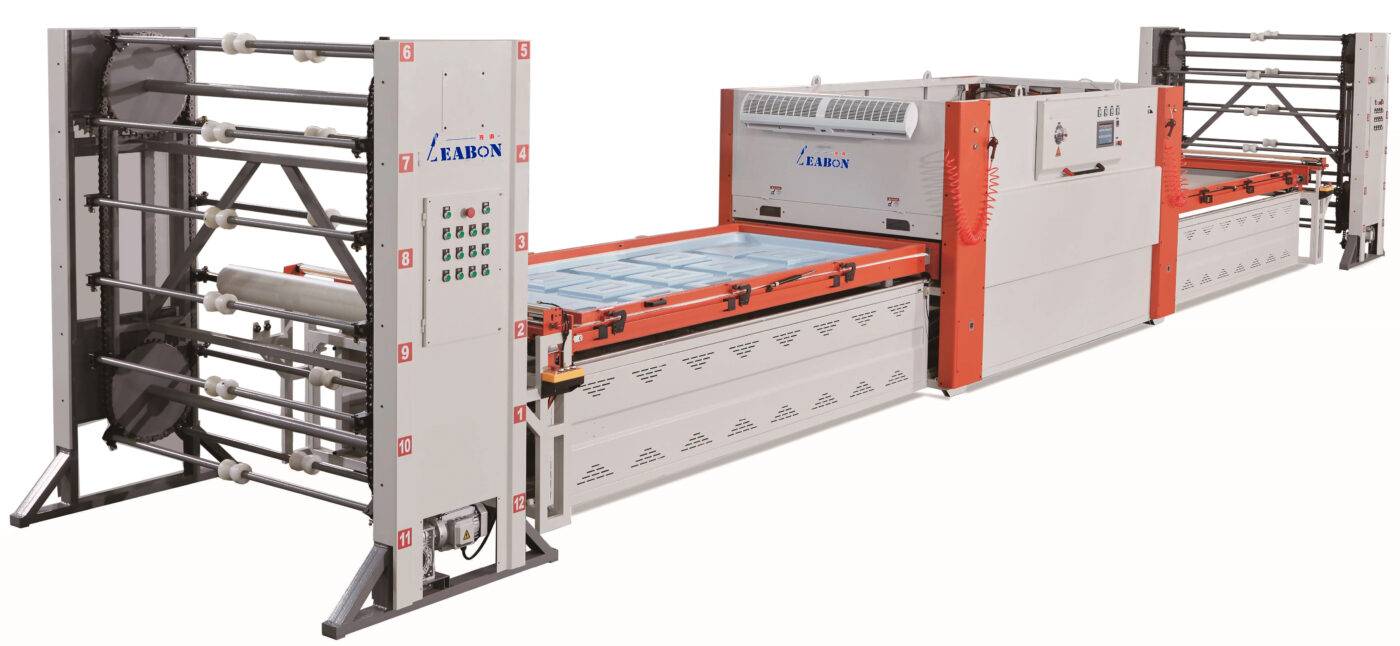
Key Types of Wood Lamination Equipment
Vacuum Laminators: Employ vacuum pressure to adhere films to curved or irregular wooden shapes, such as chair components.
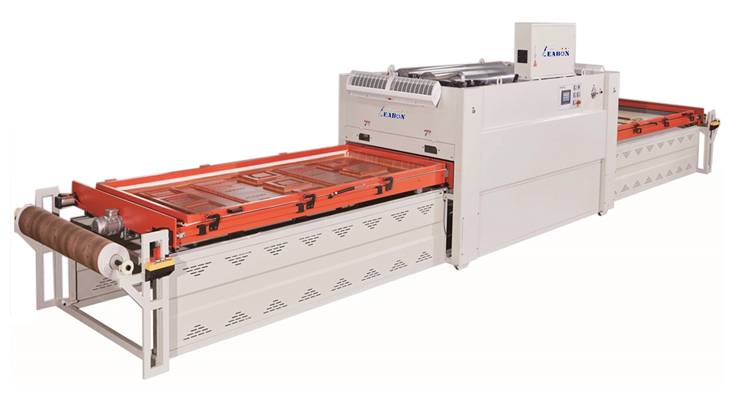
Flatbed Laminators: Ideal for applying laminates to large, flat surfaces like tabletops or wall panels.
Roller-Based Machines: Use conveyor-fed systems for continuous bonding of laminates to plywood, MDF, or particleboard.
Applications in the Woodworking Industry
-
Furniture Manufacturing: Adds scratch-resistant, waterproof layers to tables, cabinets, and shelves.
-
Flooring Production: Bonds protective wear layers to engineered wood flooring.
-
Architectural Elements: Creates weather-resistant exterior cladding and interior decorative panels.
-
Craftsmanship: Enhances wooden art pieces with metallic or textured films.
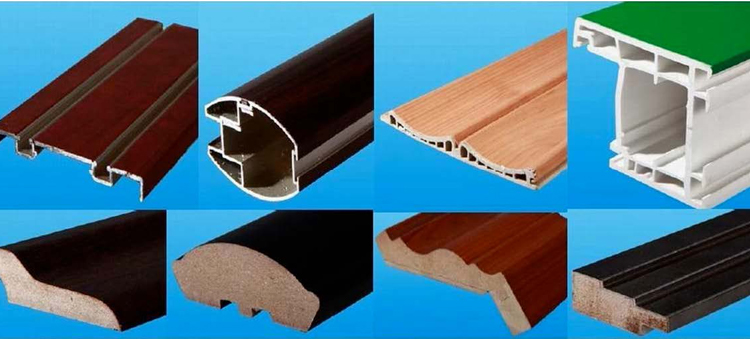
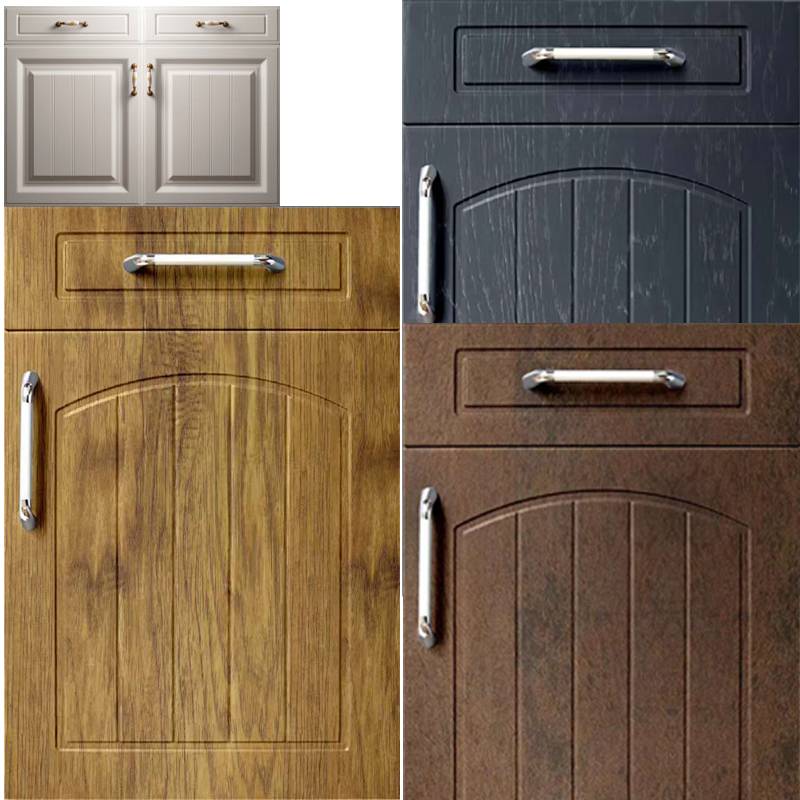
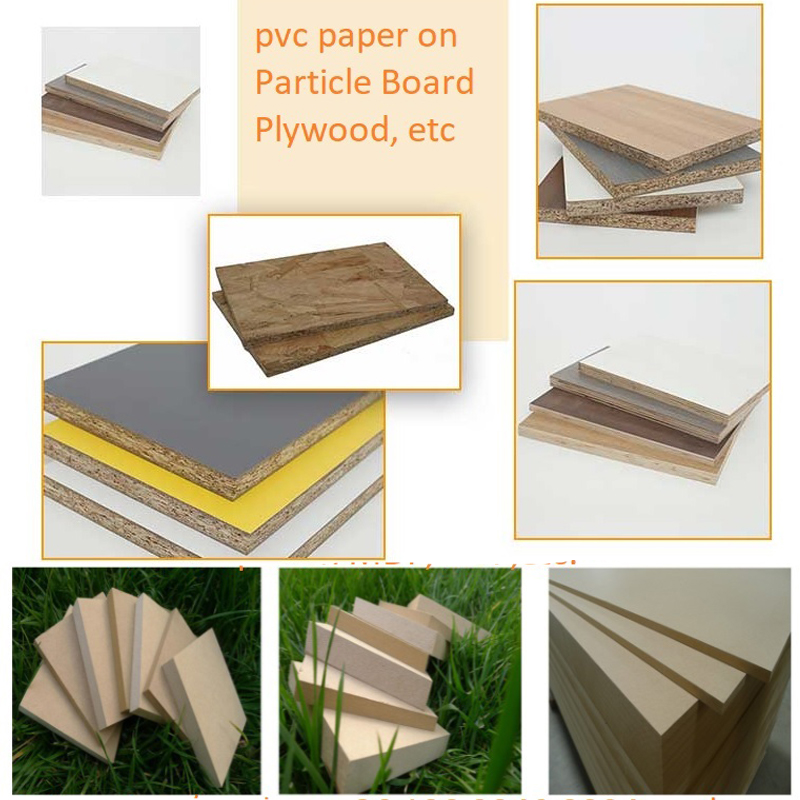
Benefits for Woodworkers
-
Enhanced Durability: Protects against moisture, UV damage, and abrasion, extending product lifespans.
-
Design Flexibility: Offers matte, glossy, or textured finishes, along with customizable patterns (e.g., woodgrain replication).
-
Cost Efficiency: Reduces the need for expensive solid wood by improving the performance of engineered wood.
-
Workflow Optimization: Automated feeders and quick-release systems minimize downtime between batches.
Choosing the Right Machine
Critical factors include:
-
Material Compatibility: Ensure the machine supports your primary substrates (e.g., hardwood, plywood, or composites).
-
Film Thickness Range: Standard options handle 0.1–5mm laminates.
-
Production Capacity: Small workshops may opt for 1.2m-wide machines, while factories require 2.5m+ models.
-
Safety Features: Look for emergency stops, overheating alerts, and dust extraction systems.
The global wood lamination equipment market is projected to grow at 6.8% CAGR through 2030, driven by demand for sustainable, high-end finishes. As hybrid materials like laminated bamboo gain popularity, these machines will remain pivotal in merging traditional craftsmanship with modern manufacturing efficiency. Whether preserving the natural beauty of oak or enabling bold, contemporary designs, woodworking lamination machines are redefining the boundaries of functional artistry in wood-based products.
To watch the video, please visit: https://youtu.be/mO_XV-4wox0